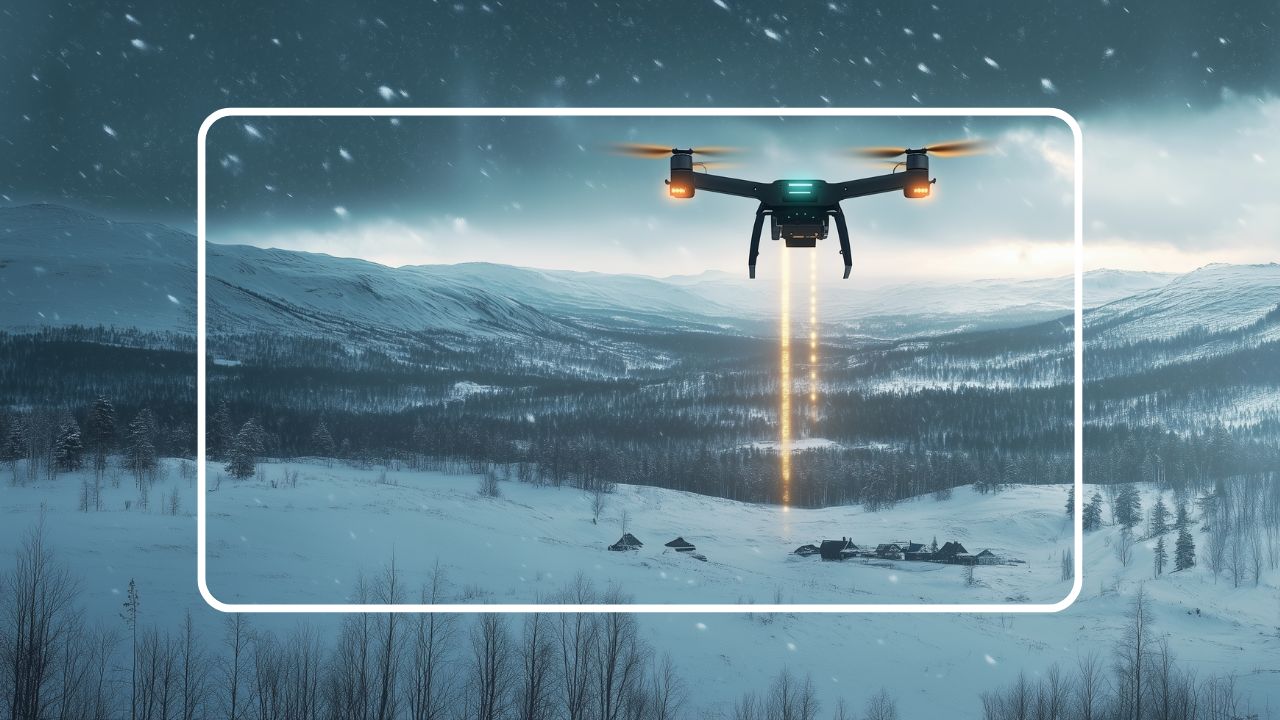
Package tracking used to entail lengthy phone calls to customer service, as well as transfers between departments in search of delivery information. These days, webhooks are quietly revolutionising modern logistics.
Our previous article defined webhooks as the foundation of modern logistics operations. We’ll now look at how real-time connectors use targeted automation to transform logistics processes.
Why automate logistics with webhooks?
Automation creates systems that scale with business growth, respond instantly to changing conditions and maintain consistency beyond what humans can achieve. The reduction in manual labour is only one benefit in a larger strategic advantage.
Webhooks excel at logistics automation due to their unique capabilities. They take immediate action when events occur, eliminating the need for scheduled checks. They connect previously isolated systems without the need for complex integration projects. The gap between status changes and responses narrows dramatically. Perhaps most importantly, they enable conditional workflows, which respond intelligently to specific events.
Three key areas demonstrate how webhook automation has transformed logistics operations.
1. Order tracking and customer communications
Silence following order placement quickly erodes customer confidence. Customers expect updates when their parcels move from ‘processing’ to ‘in transit’ or ‘out for delivery’ to ‘delivered’. Webhooks deliver this information in real time, right when the status changes occur.
Webhooks improve customer communication by triggering actions at critical points along the delivery journey. They automatically send personalised SMS or email notifications as shipments progress. Order tracking pages are updated instantly, without the need for manual intervention. Customers receive proactive alerts about potential delays before they occur. Post-delivery feedback requests arrive at an optimal time for customer response.
This proactive approach significantly reduces ‘Where is my order?’ (WISMO) enquiries. According to evidence from the logistics sector, automated tracking notifications can reduce customer service contacts by about 30%, freeing up teams to address more complex issues that require human expertise.
2. Exception management
Weather delays, vehicle breakdowns and address complications all cause disruptions to deliveries, despite meticulous planning. The speed with which these exceptions are identified and addressed determines whether they remain minor hiccups or become customer service disasters.
Exception management is a key strength of webhook implementation. They notify team members immediately when delivery exceptions occur, reducing the time between problem and awareness. When packages are delayed, automatic re-routing workflows kick in to keep delivery momentum going. Customer communications begin proactively about exceptions, preventing complaints. Support tickets are generated with comprehensive delivery information already included, saving valuable response time.
This capability provides an operational safety net for logistics systems. Problems that would otherwise cause significant disruptions are identified and resolved in a short period of time, often before customers are aware of the issues.
We spoke with an operations director at a large distribution company, who explained the business impact: “Customer retention is dependent on our problem resolution. Webhook automation allows us to identify issues quickly and implement solutions before they worsen, preserving customer relationships during difficult times.”
3. Inventory and fulfilment optimisation
Warehouse operations and delivery tracking are typically conducted in separate systems, resulting in inefficiencies and stock discrepancies. Webhooks break down silos by enabling continuous information flow between previously disconnected processes.
The return process exemplifies this integration well. When a webhook detects a return in transit, it updates inventory systems to reflect the incoming stock. Warehouse teams receive notifications to prepare receiving procedures. Stock forecasts and ordering schedules are updated automatically. Return processing forms are pre-populated, which speeds up the handling process.
This synchronisation ensures that inventory systems reflect actual conditions rather than projected scenarios. Companies with complex omnichannel operations or high return volumes benefit most from real-time accuracy.
Implementation best practices
Webhook automation necessitates careful planning and ongoing management beyond technical configuration. Successful implementations focus on four key areas:
- security
- error handling
- system integration
- and performance monitoring.
Security first
Webhooks establish external connections to internal systems, putting security first. Comprehensive security implementations protect these channels with a variety of measures. HTTPS/TLS encryption should protect all webhook communications and prevent data interception. Authentication mechanisms such as API keys and OAuth ensure the validity of incoming webhook data. IP whitelisting limits access to trusted sources in sensitive implementations. Payload validation checks incoming data for potential security threats before it’s processed.
Error handling and reliability
Webhook failures can disrupt critical business processes if proper contingency plans aren’t in place. Robust error handling begins with retry mechanisms that utilise exponential backoff to manage temporary outages. Alerting systems should notify technical teams of persistent webhook delivery failures. Comprehensive logs of webhook activities make troubleshooting easier when problems arise. Dedicated webhook management platforms add reliability to mission-critical processes.
Integration into existing systems
Most logistics operations use multiple established systems. Webhook integration must respect and enhance this complex ecosystem’s capabilities.
- Begin by mapping all systems that require webhook communication pathways.
- Document data formats and the transformations required between different systems.
- Consider version changes in connected platforms that may affect webhook functionality.
- Think about middleware solutions for highly complex integration requirements involving multiple systems.
Testing and monitoring
Continuous visibility into webhook performance ensures operational reliability. Create a testing environment that accurately represents production conditions for validation. Monitor webhook delivery rates and response times to detect any potential performance degradation. Set up alerts for unusual patterns or systematic failures that require intervention. Conduct regular audits of webhook configurations as business requirements change over time.
Real-world impact: Beyond efficiency
Webhook automation provides measurable benefits across multiple business dimensions. While specific outcomes differ depending on the implementation scope and organisational context, successful deployments produce consistent patterns.
Customer service operations typically report significant reductions in WISMO queries, with many organisations experiencing decreases of 25-40%. This represents both cost savings and an improved customer experience.
(Learn more about the broader business impact of WISMO queries and how to address them strategically.)
Exception resolution times are dramatically reduced, from hours to minutes, thanks to automated alerts and responses. Inventory accuracy improves significantly, resulting in fewer costly stockouts and excess inventory carrying costs. Customer satisfaction scores are rising as delivery experiences become more transparent and dependable. Operational costs are reduced through more efficient resource allocation and reduced manual intervention.
The most noticeable results come from organisations that use webhooks as part of a comprehensive strategy. Instead of automating isolated processes, these companies build interconnected ecosystems in which information flows seamlessly between previously siloed systems, amplifying the benefits throughout the operation.
Getting started with webhook automation
Webhook automation transforms logistics operations in a structured manner that minimises risk while maximising impact. Begin by thoroughly mapping current logistics processes, identifying manual touchpoints and information bottlenecks that cause delays in operations. These are ideal opportunities for initial automation efforts.
Evaluate potential automation opportunities by weighing business impact versus implementation complexity. This analysis assists in prioritising projects that provide the most value while having reasonable implementation requirements. Instead of attempting comprehensive changes all at once, start with a focused webhook implementation that addresses a single key process. This approach enables teams to gain expertise and improve implementation methods.
Measure results against well-defined KPIs to quantify progress and gain organisational support for additional automation. Once the initial implementation demonstrates success, scale gradually to additional processes, applying lessons learned from earlier deployments to improve subsequent implementations.
The future is connected
Logistics evolution favours organisations that can adapt quickly, scale efficiently and deliver exceptional customer experiences despite volume fluctuations. Webhook automation is more than just a technical implementation; it offers a strategic advantage through operational agility and responsiveness.
Webhooks enable truly responsive logistics operations by establishing strong connections between systems, events and actions. Forward-thinking organisations recognise the competitive necessity of webhook automation and instead prioritise strategic implementation sequencing.
Explore how webhook automation can transform your logistics operations. Contact Sorted today for a personalised consultation tailored to your specific business requirements.